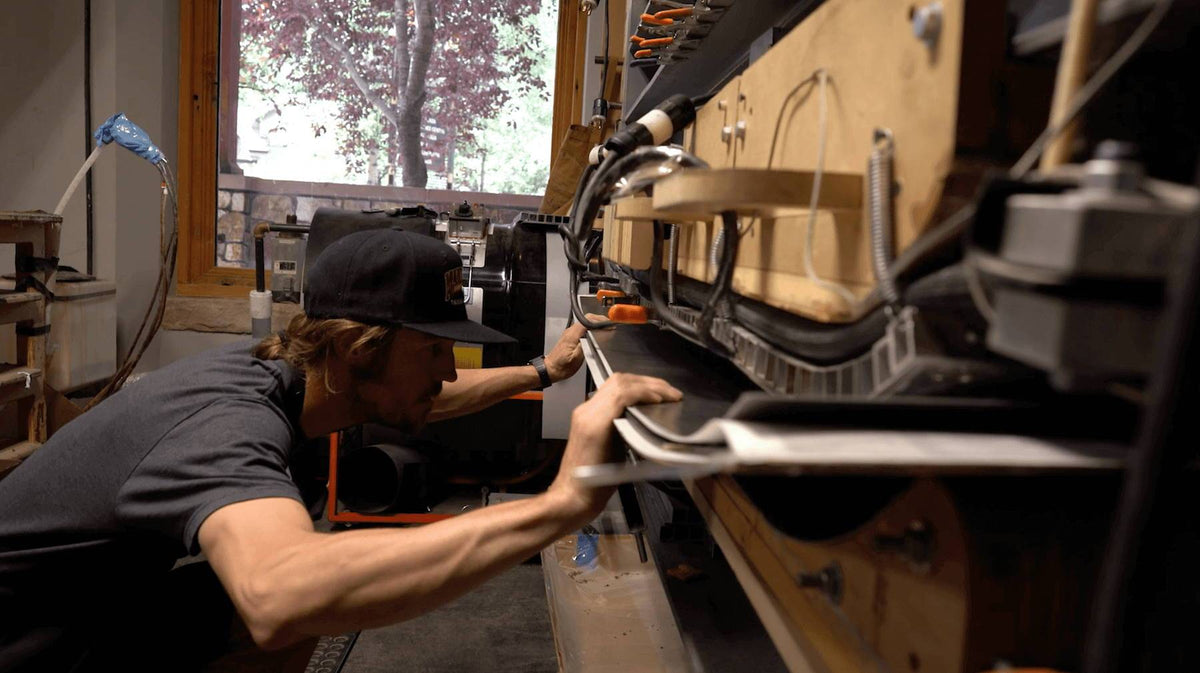
Wagner Factory Tour: The Ski Press
Once we have fabricated the components of a ski, we will do what is called a wet layup process. This process involves taking each component of the ski, starting with the base, and stacking the structural layers while applying resin between each layer. The final piece of this process is adding the topsheet. We then put a steel cassette on top of that “sandwich” of ski components and slide that ski block into our ski press.
The ski press is a unique piece of technology that cooks the ski so that all the structural materials bond together. First, we adjust the length of the press by adding and removing different spacer blocks. Next, we select the correct tip and tail blocks for the ski. These are determined by our design tool, and the code will communicate these instructions to the ski builder. We have different tip and tail blocks that will work with various types of ski designs. Once these have been chosen, we insert the correct block that puts the camber or rocker on the skis.
After all the correct blocks are chosen and inserted, we slide the ski block into the press which has has a heating element in the top and the bottom. We then inflate the airbags which apply pressure and “cook” the skis. Once this process is complete, we pull the skis out of the press as one block, two skis side by side. The next step in our ski building process becomes extracting the skis from the block and turning them into a pair of high performing skis.
Are you curious what elements would make up your ski press? Get started on your custom journey by scheduling a call with a ski designer.
Want to learn more about our process? Take a look at other parts of our factory tour here:
Skier DNA
Graphics
Wood Cores
Base Materials and Steel Edges
Structural Materials
Ski Finishing and Tuning
Mounting and Bindings
--