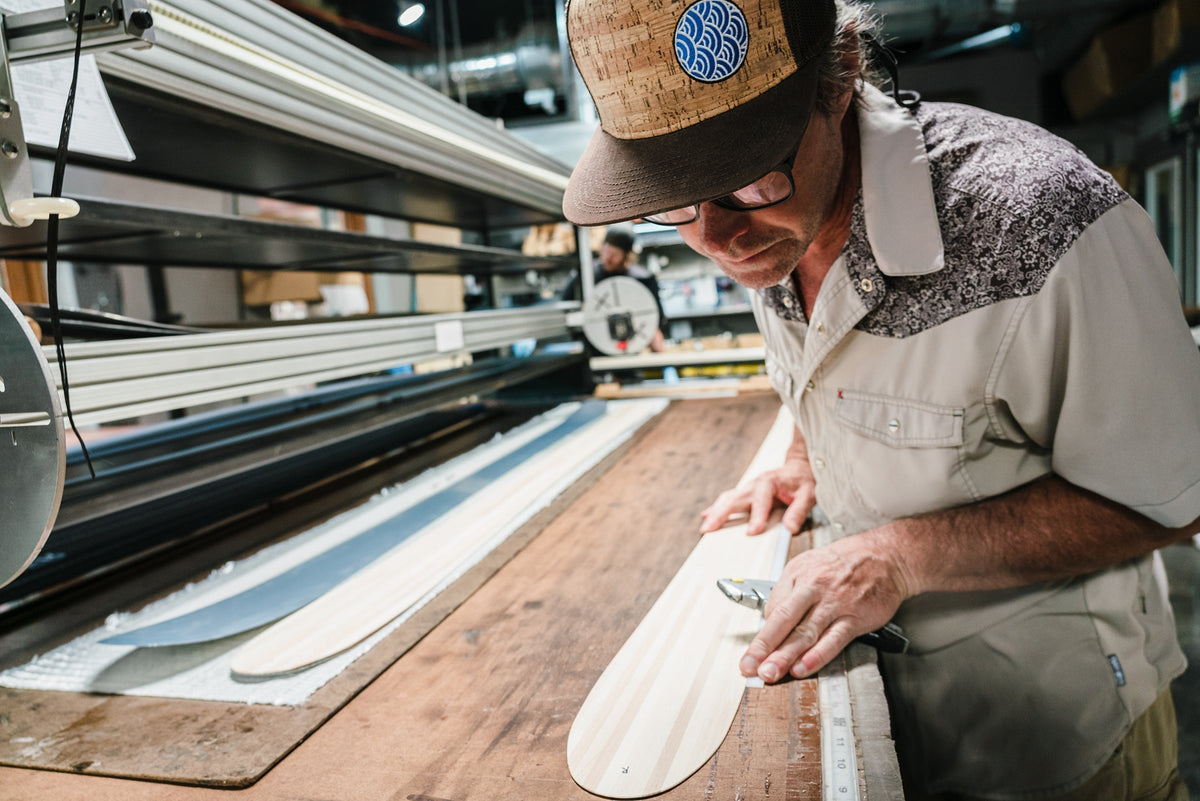
Where Your Skis Are Made Matters
When it comes to ski performance, most brands tout their latest tech.
But what many brands don’t really talk about is where their skis are actually made. And, just like it does with automobiles or bikes or boats, the factory matters.

Dave Chew inspects some skis on the CNC bench.
The underbelly of the ski industry is a complicated web of supply chain, brand identity, and the bottom line, which ultimately drives the entire operation. Some brands proudly fly a national flag—Blizzard, Stöckli, and Dynastar, to name a few—but most operate out of several factories in more affordable places like Eastern Europe and China, outsourcing lower-end skis to lower-cost factories to make the numbers work.
The biggest problem in lower-cost factories is quality control. While bigger brands that have the budgets and staffing to pay attention to what’s happening on the ground in the factories, smaller brands that don’t have the staffing and budget struggle to do so. (We reached out to several brands to ask them to weigh in on the specifics*, but none wished to comment. Which, of course, speaks volumes.)
*Editor's note: One company wouldn’t even tell Kim on the record what COUNTRY they make their skis in.

Cormac Bourke lays down some metal.
Every aspect of ski construction affects its performance. Temperature, pressing time, and material handling all influence how materials bond and how the final product behaves on snow. Mass production facilities rush skis through assembly to meet quotas.
At Wagner Custom, however, we design and build all of our skis right here in our Telluride, Colo., factory. We oversee every single aspect of the process, and we have our hands directly on your skis from start to finish. We feel so strongly about the quality of our materials and our ski-building integrity that we encourage visitors to come tour our factory with us to see how the magic happens.
Our factory's single-batch approach means every pair of skis receives meticulous attention. Each production stage is visible and accountable. There's no mystery about who pressed your skis or how long they cured—we know because we were there.

Scott Hargreave works on some cores.
The result? Skis that perform exactly as designed, with consistent flex patterns, proper torsional rigidity, and durability that lasts season after season. That's the Wagner factory difference.
Ready to experience factory-direct performance? Design your custom skis today.
Want to learn more about the people who build your skis? Find out more here and here.
--
Article by Kimberly Beekman
Kimberly Beekman is the former editor-in-chief of the late, great Skiing Magazine (RIP), and a longtime editor of SKI Magazine before that. She currently uses the title of “freelancer” as a beard to ski powder all over the world. She lives in Steamboat, Colorado, with her wonderful daughter and terrible cat.